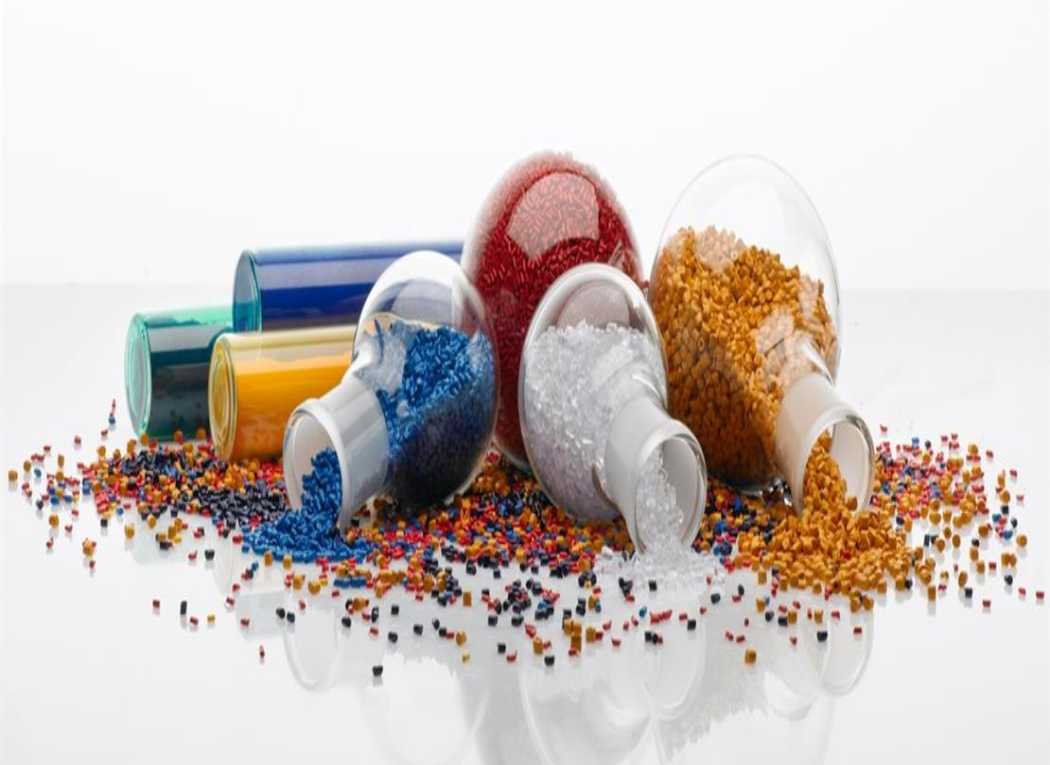
گرانول، محصول نهایی دستگاه گرانولساز میباشد. گرانول به شکلی از مواد پلیمری میگویند و بیانگر نوع یا جنس پلیمر نمیباشد. گرانول های پلاستیکی به دو شکل عدسی و رشته ای تولید میشوند و از نظر کیفیت نهایی با هم تفاوتی نداشته و این تفاوت صرفا در شکل آن ها میباشد. گرانول پلاستیک بعنوان مواد اولیه در تقریبا تمامی قسمت های صنعت پلاستیک قابل استفاده میباشند. به عنوان مثال ؛ در صنایع تولید فیلم و نایلون و تولید قطعات پلاستیکی و آمیزه سازی و تولید لوله و …
گرانول ، به وسیله دستگاه گرانول ساز که نوعی اکسترودر میباشد، ساخته میشود و مواد اولیه این دستگاه شامل پرک شست و شو شده و مواد بازیافتی کندر شده و پودر و …. میباشد .
دستگاه گرانول ساز به چه صورت کار میکند؟
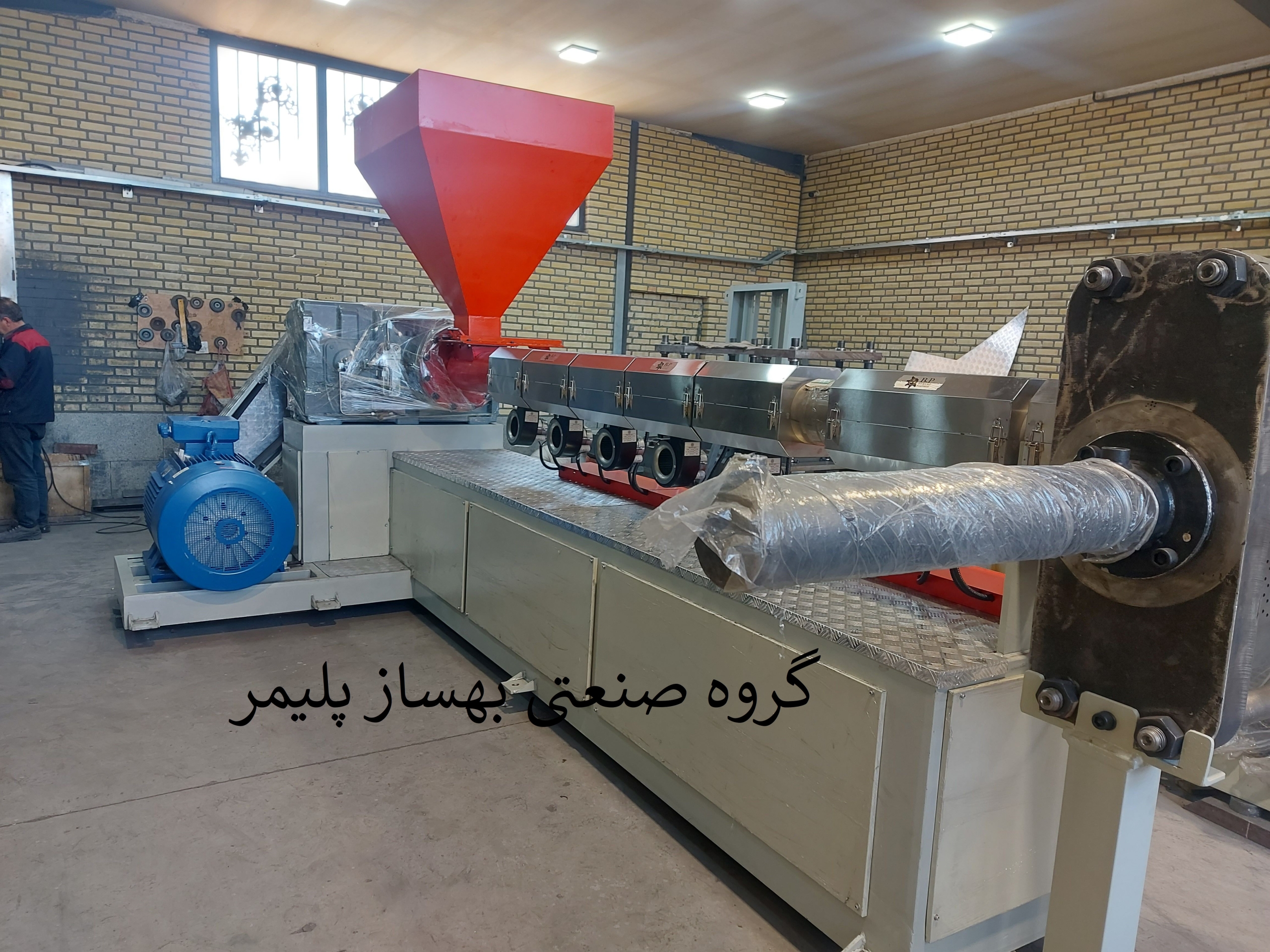
دستگاه گرانولساز ، دستگاهی شبیه به چرخ گوشت میباشد که مواد اولیه پلاستیک به آن داخل میشود و در سیلندر بر اثر کرمای هیترها ذوب شده و مذاب به وسیله مارپیچ به قسمت انتهایی یا دای (DIE) منتقل میشود. در دای (DIE) ، مذاب شکل قالب را به خود گرفته و به صورت رشته های ماکارونی شکل، وارد حوضچه آب میشوند و در آنجا سرد شده و بسمت خردکن یا کاتر منتقل میشوند.
معرفی قسمت های اصلی دستگاه گرانول ساز :
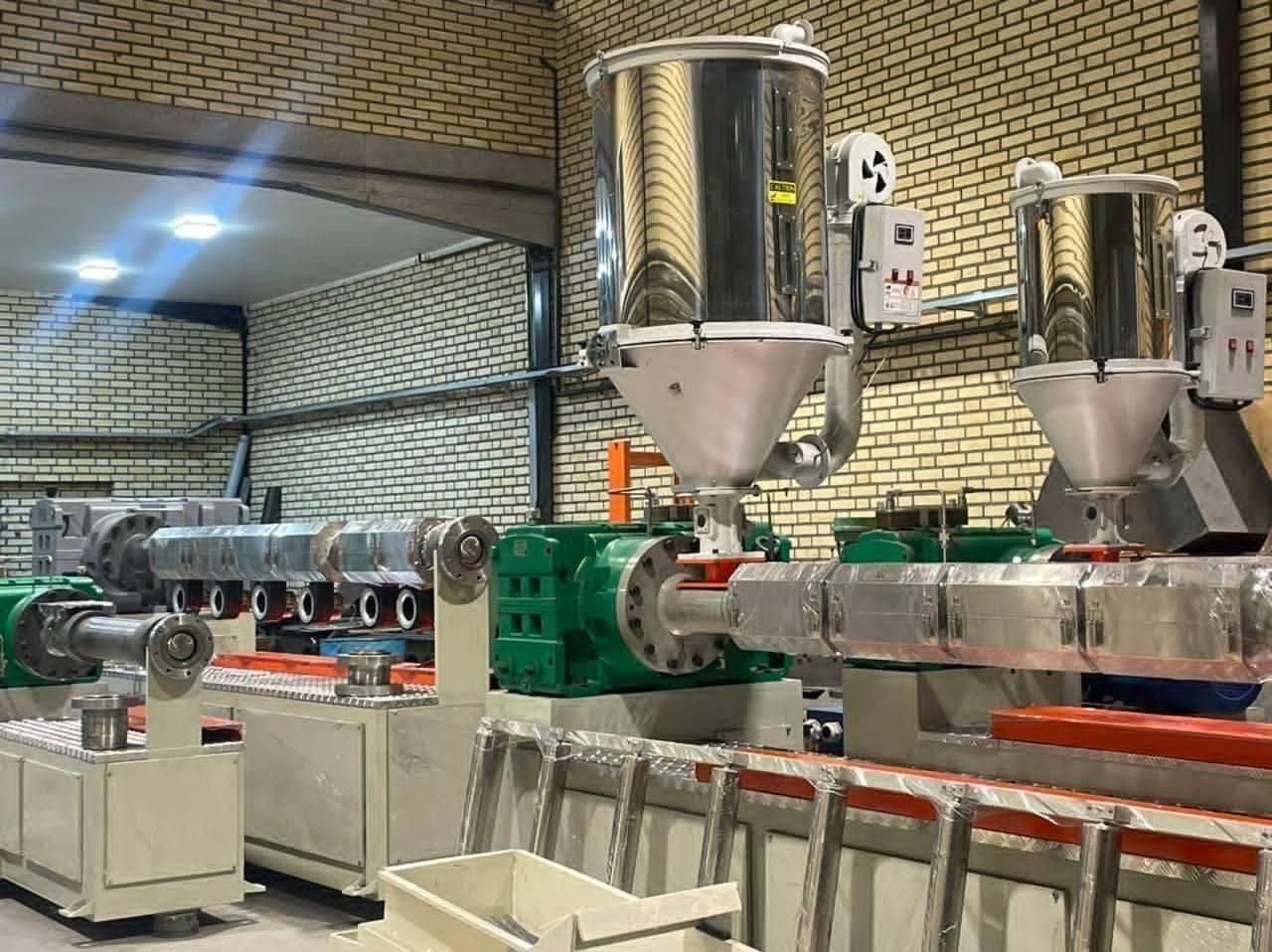
1 ) قیف تغذیه دستگاه گرانول ساز
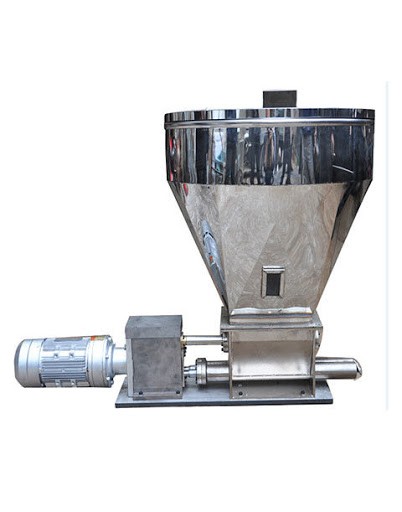
شامل یک قیف فلزی که مواد در آن ریخته میشوند و وظیفه خوراک دهی به دستگاه را دارد.
2 ) سیلندر ماردون ( سیلندر مارپیچ )
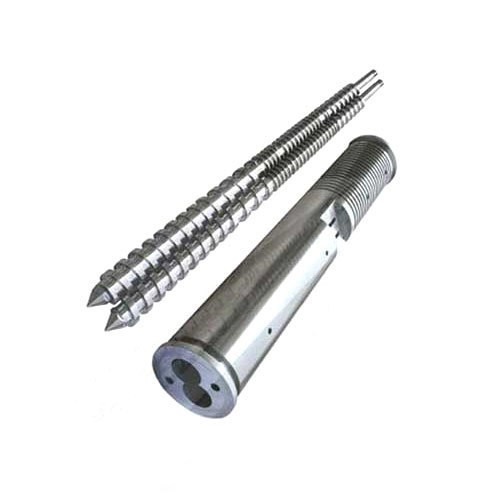
3 ) سیلندر ( Barrel )
یک استوانه فلزی توخالی میباشد که مارپیچ داخل آن قرار میگیرد و در لایه بیرونی سیلندر هیترها قرار میگیرند، منجر به ذوب شدن مواد پلاستیکی میشوند.
مارپیچ ( screw ) :
این قسمت ، مهمترین قسمت دستگاه میباشد و وظیفه انتفال و اختلال مذاب را به عهده دارد .
4 ) دای ( die )
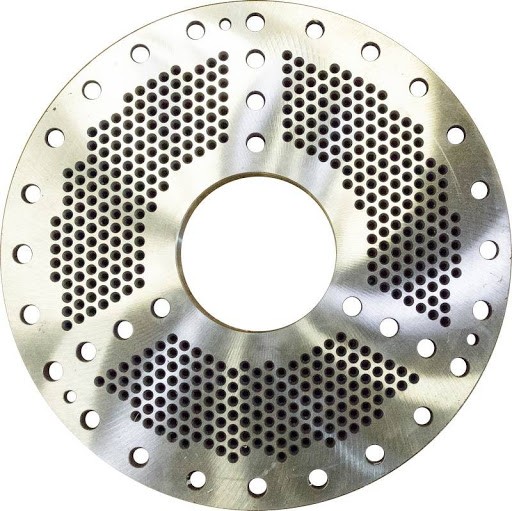
این قسمت در انتهای سیلندر قرارگرفته است و مذاب از این ناحیه خارج میگردد
5 ) گازگیر و رطوبت گیر
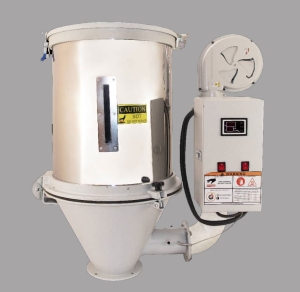
این قسمت در یک سوم انتهایی سیلندر قرار میگیرد و در واقع یک حفره در بدنه سیلندر ایجاد شده است که گاز موجود در مواد از آن خارج شود.
انواع دستگاه گرانول ساز :
در کل میتوان گفت ک دستگاه گرانول ساز به سه نوع اصلی تقسیم بندی میشوند :
دستگاه گرانول ساز تک مارپیچ
دستگاه گرانول ساز تک مارپیچ ، شامل یک مارپیچ میباشد که اغلب برای ساخت گرانول از مواد بازیافتی بکار میرود.
دستگاه گرانول ساز دو مارپیچ :
دستگاه گرانول ساز دو مارپیچ ، متشکل از دو مارپیچ موازی در کنار هم تشکیل شده است. موارد استفاده این دستگاه اغلب برای ساخت مستربچ و کامپاند های پلیمری صورت میگیرد . مذاب در اثر حرکت این دو مارپیچ به جلو حرکت میکند و امکان اختلاط با انواع پودر های افزودنی در آن وجود دارد . معمولا ظرفیت تولید این گرانول ساز ، از توع تک ماردون بیشتر است. البته به مراتب ، قیمت بالاتری هم دارد.
دستگاه گرانول ساز دو مرحله ای :
دستگاه گرانول ساز دو مرحله ای ، در واقع از دو دستگاه اکسترودر در راستای یکدیگر تشکیل شده است. مواد مذاب از دستگاه اول به دستگاه دوم ریخته می شود. این دستگاه مناسب برای مواد بازیافتی است که دارای رطوبت بالایی برخوردار میباشد و در دستگاه های تک مرحله ای، امکان گازگیری کافی وجود ندارد. برای ساخت گرانول از موادی نظیر پلی آمید، بهتر است از دستگاه گرانول ساز دو مرحله ای استفاده شود.
بررسی عوامل موثر بر کیفیت نهایی گرانول تولیدی
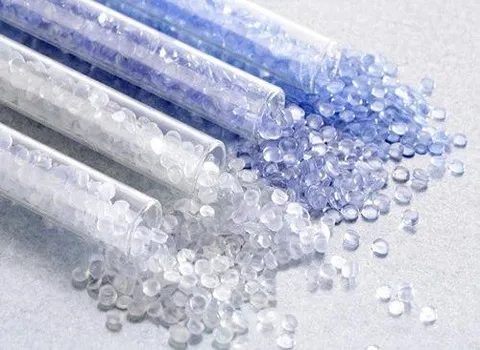
کیفیت مواد اولیه :
مواد اولیه دستگاه گرانول ساز ، اغلب شامل مواد بازیافتی میباشد که در مراحل قبلی بازیافت ، شسته شده و بصورت پرک در آمده است. با کیفیت بودن این مواد نقش اساسی در کیفیت گرانول و حتی روان بودن پروسه تولید گرانول دارد.
جداسازی و تفکیک :
این مرحله، جزو اصلی ترین نقش را در کیفیت گرانول تولیدی دارد. ، ضایعات پلاستیک در ابتدا به صورت مکانیکی یا دستی تفکیک میشوند و به عنوان مثال ، ضایعات پلی اتیلن نباید با ضایعات ABS به صورت همزمان وارد خط بازیافت شوند. پس در مرحله اول پلاستیک هایی که از یک جنس نبوده بایستی از هم تفکیک شوند و جداسازی صورت گیرد. البته در مواقعی، حتی با اینکه جنس ضایعات از یک نوع پلاستیک هست اما نباید با هم ترکیب شوند. به عنوان مثال ، ضایعات نایلون و لوله مشکی، هردو از جنس پلی اتیلن هستند اما از دو گرید متفاوت پلی اتیلن ساخته شده اند. هر یک از این گرید ها دارای MDI و وزن مولکولی متفاوتی میباشند و چنانچه به طور همزمان وارد دستگاه گرانول ساز شوند، مشکل ایجاد میشود.
تمیز بودن مواد :
تمیز بودن مواد و عدم وجود ناخالصی، از دیگر مواردیست که در کیفیت گرانول تولید شده به وسیله دستگاه گرانول ساز، تاثیر بسزایی داشته، مواد تمیز، پروسه تولید گرانول را روان تر میکند و سبب قطع شدن رشته نمیشود، چنانچه مواد شست و شو نشده ، گرانول شود، برای مصرف کننده گرانول هم در هنگام تولید گرانول و هم در کیفیت محصول نهایی تاثیر به سزایی میگذارد. به عنوان مثال ، گرانولی که از مواد شست و شو نشده ساخته شده باشد، در پروسه تولید نایلون و فیلم ، منجر به پارگی دایم فیلم در پروسه تولید میشوند. همچنین قطعات تولید شده با این گرانول ، بسیار شکننده خواهند بود.
خشک بودن :
قبل از این که مواد را به داخل دستگاه گرانول ساز تغذیه کنید، از خشک بودن صد درصدی مواد اطمینان حاصل نمایید. موادی که دارای رطوبت هستند، بعد از این که وارد دستگاه گرانول ساز میشوند گاز خود آزاد میکنند. چنانچه دستگاه شما گازگیر داشته باشد، بخشی از این رطوبت ، از طریق گازگیر خارج میشود و بخش دیگری در داخل گرانول تولید شده محبوس میشود و سبب بی کیفیت شدن گرانول شما میشود.
دستگاه گرانول ساز
نکته دیگری که در کیفیت گرانول تولیدی شما تاثیر گذار است، کیفیت دستگاه گرانول ساز است. طراحی ماردون این دستگاه ها بر طبق جنس پلاستیک مورد مصرفی صورت میگیرد. به عنوان مثال، در طراحی ماردون، برای مواردی نظیر نایلون، عمق گام مارپیچ را کم در نظر میگیرند. جنس ماردون ، بایستی از فولاد ضد زنگ باشد. اغلب سازندگان دستگاه گرانول ساز از فولاد VCN جهت ساخت ماردون استفاده میکنند.
جهت تولید گرانول با کیفیت، شما بایستی از فیلتر یا توری دستگاه گرانول ساز استفاده نمایید . نقش توری یا فیلتر ، جداسازی ناخالصی های باقی مانده در مذاب پلیمر میباشد. جنس این ناخالصی ها میتوانند از مواد غیر پلیمری یا مواد پلیمری که از نقطه ذوب بالاتری برخوردارند و ذوب نشده اند، باشد. فیلتر های دستگاه گرانول ساز اغلب از سایز 40 تا 120 درجه بندی میشوند و هر چه قدر این درجه بالاتر باشد، منافذ فیلتر ریز تر خواهند بود و جداسازی بهتر صورت میگیرد.